Refrigerated transport is a $31 billion industry with revenue growth at an annualized rate of 3.2% in the U.S. This vital industry fulfills the critical role of hauling temperature-sensitive goods such as groceries, pharmaceuticals, flowers and other perishable freight. Trucks with refrigerated trailers, also known as reefers, have built-in refrigeration systems to provide consistent low temperatures that prevent goods from spoiling and keep store shelves stocked.
When you need to ship temperature-sensitive goods, asking the right questions can be the difference between successful transport and ruined goods. Let’s look at the top five questions to ask about refrigerated transport services.
1. How Do the Reefer Trucks Meet Food-grade Requirements?
If you’re hauling food products, you’ll need refrigerated transportation that closely follows best practices and has proper features to ensure safety. Questions to ask include:
• Will the trailer undergo a precooling process?
• Will the trailer be disinfected before goods are loaded?
• Does the truck have food-grade, antimicrobial surfaces to help prevent contamination and bacteria growth?
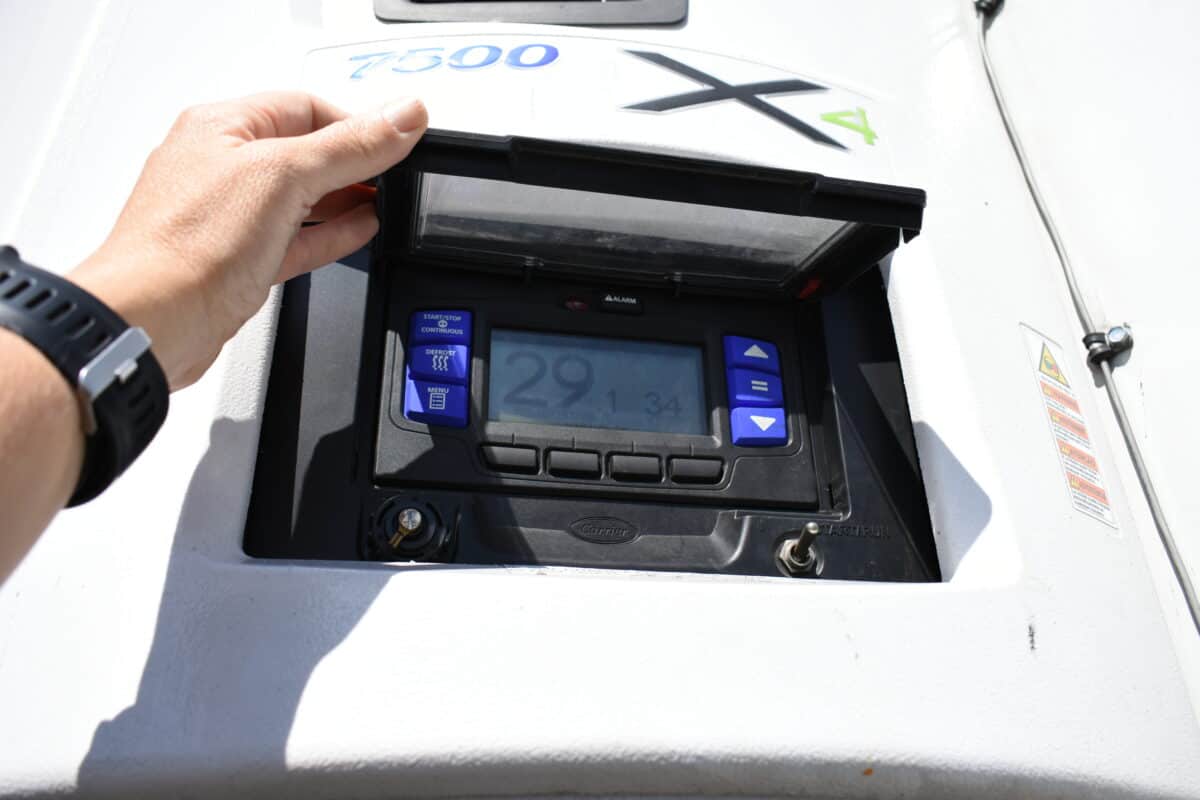
2. Are Industry Standards and Regulations for Refrigerated Transport Being Met?
Government guidelines help ensure safety for your goods. Ask for compliance statements to ensure government standards are being followed, including:
Food Safety Modernization Act (FSMA)
The FSMA is designed to prevent foodborne illnesses from originating along the supply chain for both human and animal food. This act prevents practices during transportation that create food safety risks, such as failure to properly refrigerate food and inadequate cleaning of vehicles between loads.
Hazard Analysis and Critical Control Points (HACCP)
The HACCP addresses food safety by managing biological, physical and chemical hazards throughout the supply chain including production, procurement, manufacturing, distribution and consumption.
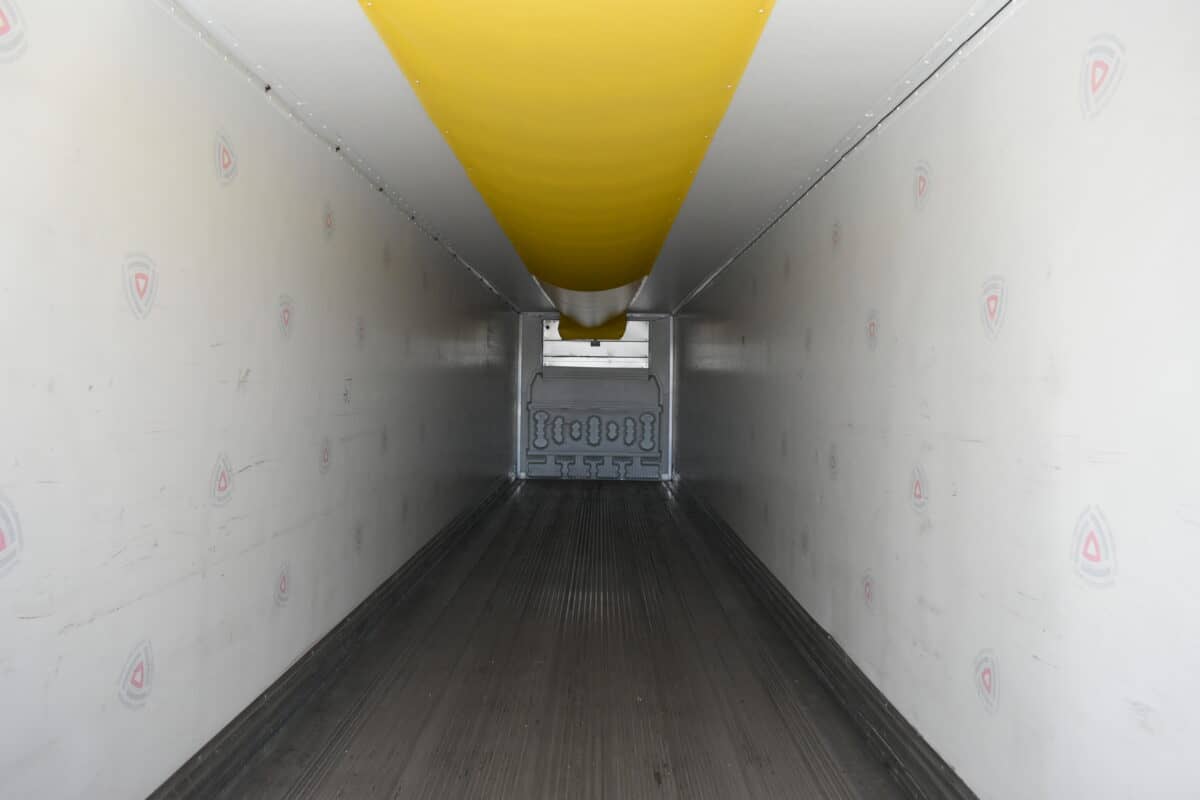
3. Will Your Products be Shipped with Another Order?
If you’re using less-than-truckload (LTL) shipping, your products may be shipped with another company’s goods. Inquire about the temperature requirements for the other load. Goods within the same shipment will be kept at the same temperature, so they must have the same requirements to avoid damage. Otherwise, your items may be kept too warm or too cold to accommodate another company’s products.
Also ask about timing and the schedule. Extra time spent handling another company’s delivery means more time your goods need to be kept at a controlled temperature. Ask if unloading the other items may affect the trailer temperature. Can a consistent temperature be maintained throughout the full journey?
4. How Closely are Temperatures and Humidity Monitored?
Even slight variations in temperature can affect product quality. Check with the refrigerated trucking company to make sure temperatures are consistently monitored throughout the duration of the trip and ask which type of technology is used. Moisture levels are also important to maintain quality. Too much humidity can lead to freight damage caused by moisture. Precise controls can keep humidity at safe levels.
5. How Well Does the Company Handle Tracking and Delivery?
Shipment tracking gives you peace of mind with the ability to monitor efficient progress and know exactly where your product is. Is tracking part of the company’s refrigerated transport services? Also ask for delivery statistics. A strong on-time delivery record is a sign of reliability.
Stay Cool with Midwest Carriers
Ensure your temperature-sensitive freight arrives safely to its destination in top condition every time. Connect with Midwest Carriers for dependable refrigerated transport.
Find Your Future at Midwest Carriers
Working for Midwest Carriers is the gift that keeps on giving. Start your new career with an employer who cares about you, your career goals and your home life. Learn more about driving for Midwest Carriers today.